Transformation of steel production: Two routes will lead to high-quality steel in the future
We continue to be a reliable producer of the highest quality steel products in premium quality. And they will be better because we will produce them with fewer CO2 emissions in the future. With greentec steel, we are creating the technical conditions for this and implementing Austria's largest climate protection programme.
High-quality steel, either way
In the future, two production routes will lead to high-quality steel. With blast furnace and converter on one side, with electric arc furnace (EAF) on the other. Both process lines have been known for many decades and have been used successfully according to their specifics. However, climate change requires a further development of the classic EAF route. While the technologically necessary, massive use of coke in the blast furnace leads to high CO2 emissions, they could be significantly reduced by the EAF – provided that sufficient green electrical energy is available on site.
The path to climate-friendly steel
In both ways, we produce recognized excellent steel. However, we can only achieve our goal of CO2-reduced production with the EAF. With greentec steel, our decarbonization program, we are gradually reducing CO2 emissions. As early as 2027, the commissioning of the first EAF in Donawitz and Linz, with the simultaneous shutdown of one blast furnace each, will ensure a 30% reduction in emissions.
The traditional route
In the process route via blast furnace and converter, which has been economically optimized for decades, iron ore is reduced to liquid, carbon-rich pig iron in the blast furnace with the addition of coke. In the LD converter, the pig iron is freed from most of the undesirable components with the help of inflated oxygen. After that, further processing takes place depending on the customer's wishes.
The EAF Path
Crude steel production via the EAF is also not new. The biggest difference to the blast furnace route is the energy and raw material sources. The use of green generated electrical energy is the essential step towards decarbonizing steel production. Instead of iron ore, scrap is mainly used on this route. Depending on availability and quality requirements, liquid pig iron or so-called HBI (Hot Briquetted Iron) can also be used. The input materials supplied are heated with an electric arc and melted down in the process. After the tapping of an EAF, the crude steel is also processed here as before in so-called secondary metallurgy.
What are the advantages of an EAF?
The use of EAF is significantly changing the landscape of our crude steel production. The advantages of its use are in particular the lower CO2 emissions:
There are also other technological advantages
- High capacity of the EAF with maximum availability and flexible process control:
a new batch takes place every approx. 50 minutes - EAFs can be "switched on/off" within a few minutes – they must of course be emptied before switching off.
- Production of the highest steel qualities through the use of correspondingly high-quality raw materials, e.g. HBI or high-quality scrap
- Flexibility in terms of input materials (scrap, HBI, pig iron)
- Quick vessel change: If the EAF needs to be rebuilt to make it refractory, it can be replaced by a second vessel – operation continues. This is not possible
with an LD converter Changeover effort: EAF approx. 8 h; Downtime LD crucible: 4-5 days.
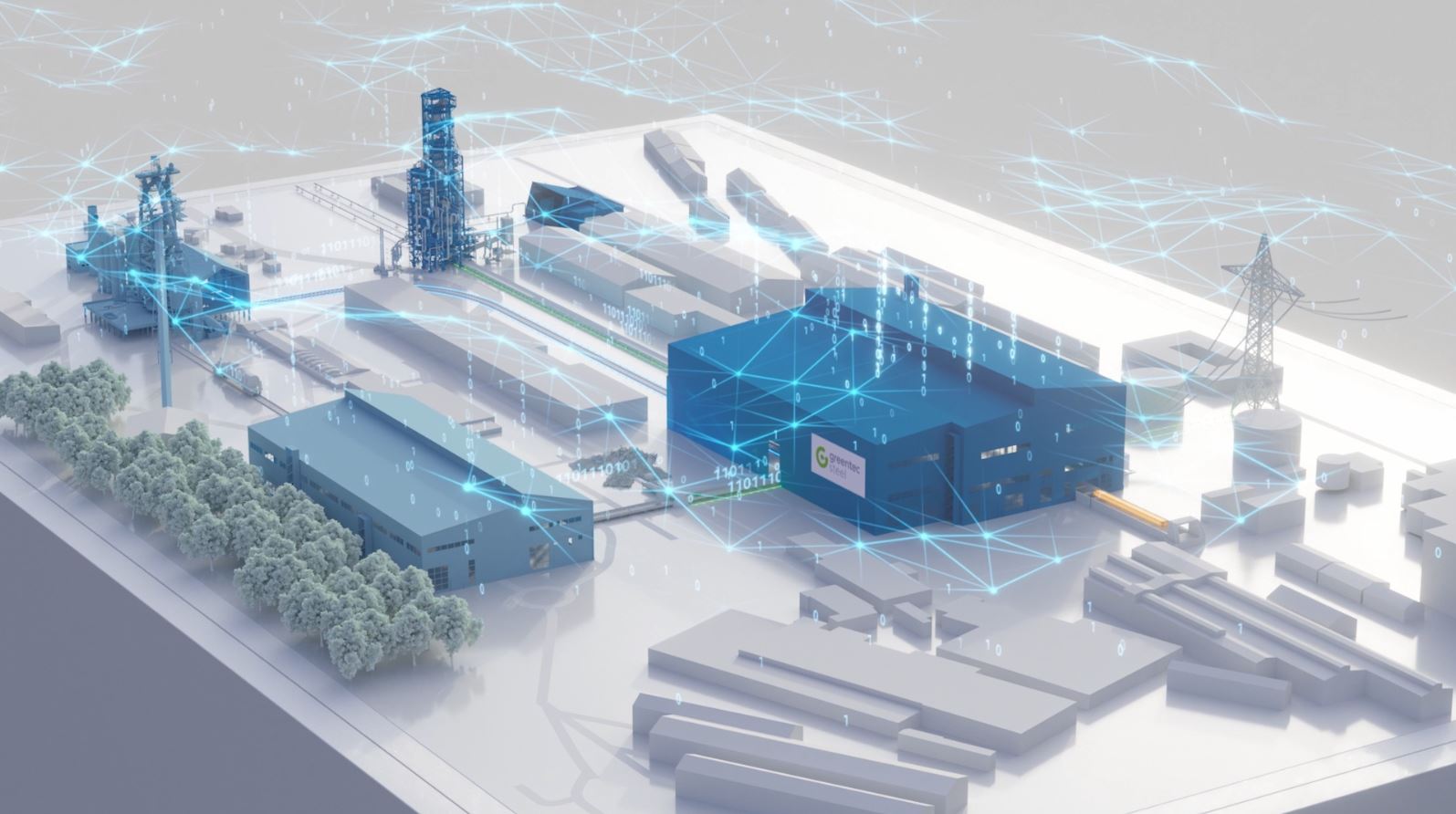
Challenges of the EAF route
The sole use of EAF technology also presents us with challenges. These include the following:
- process gases from the coking plant, blast furnace and LD steelworks are no longer available for their own electricity generation;
- the EAF is less able to remove the steel pest sulphur (introduced by input materials). Its removal requires a greater effort in secondary metallurgy.
- Scrap contributes far more trace elements to steel production than ores. Their enrichment affects the technological properties of the steel.
At voestalpine, we are also working on technologies in research and development to be able to deal with these challenges. For example, we are improving the possibilities of scrap processing and sorting.